Within the broad scope of industrial, electronic, and consumer applications, micro switches, despite their compact form factor, enable critical functional control. Selecting the appropriate micro switch for a specific application is paramount to ensuring stable system operation and meeting diverse functional requirements. This article aims to comprehensively explain the process of precisely matching the optimal micro switches according to differing application landscapes and technical imperatives, with the objective of offering a practical and instructive selection guide for engineers, designers, and associated experts. Our exposition will cover critical selection specifications, application-related considerations, and potential design refinements, all geared towards facilitating informed decision-making for readers navigating the complexities of the micro switch market.
Understanding Critical Technical Specifications for Micro Switch Selection
Micro switches are precise electromechanical assemblies that facilitate rapid and dependable switching of contact sets through minimal mechanical displacement. Their principal merits lie in high sensitivity, superior actuation accuracy, extended mechanical lifecycle, and robust electrical endurance, rendering them a preferred component for diverse applications with stringent reliability and durability criteria. Their core technical specifications primarily comprise rated voltage and current, contact configuration (normally open – NO, normally closed – NC, changeover – COM), electrical life, mechanical life, operating force, and release force.
A comprehensive understanding and command of these fundamental characteristics represent the primary and crucial phase for accurate selection, akin to a thorough evaluation of the physicochemical properties of engineering materials prior to their integration. By way of illustration, the rated voltage of a micro limit switch must exhibit strict compatibility with the voltage rating of the intended application circuit; selection of an excessively high voltage can precipitate unreliable contact closure or interruption, potentially culminating in dielectric breakdown, while selection of an insufficient voltage can induce contact overload, intermittent conduction, or operational anomaly, significantly jeopardizing system safety and dependability.
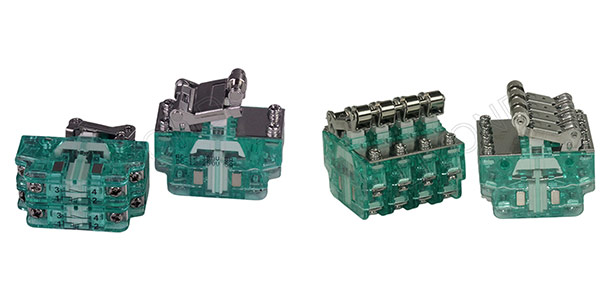
Application-Based Micro Switch Selection
Micro Switch Selection for Industrial Automation
In highly integrated automated manufacturing systems, micro switches serve as critical sensing elements, being widely deployed for precise limit control, workpiece position sensing, and safety interlock mechanisms.
For such high-actuation frequency applications, the primary engineering consideration is the micro switch’s mechanical lifecycle, typically necessitating millions or even tens of millions of operational cycles to ensure the protracted stable functioning of the manufacturing line. Within high-end equipment manufacturing, precision instrumentation, and analogous domains with exceptionally stringent positional accuracy requisites, preference should be accorded to micro switches exhibiting superior repeatability and minimal hysteresis characteristics, often with repeatability specifications within the micrometer regime. This assures highly consistent actuation points, thereby mitigating error accumulation in manufacturing or measurement procedures and securing product quality and dependability.
Moreover, challenging industrial environments frequently involve intricate elements such as dust, oil contamination, significant vibration, and potential electromagnetic interference (EMI). Therefore, micro switches featuring robust ingress protection (IP Rating, such as IP67 or greater), exceptional vibration resistance (meeting relevant industrial norms), and effective electromagnetic interference immunity should be chosen, alongside consideration of the operating temperature range suitability for the application. This effectively mitigates contaminant ingress that could compromise contact conductivity reliability or spurious actuation due to mechanical vibration and electromagnetic interference, ensuring the protracted stable and dependable operation of automated manufacturing systems.
Micro Switch Selection for Appliance Applications
Within home appliance products, including microwave door interlocks, washing machine safety switches, and refrigerator light switches, micro switches typically serve in crucial roles such as safety status monitoring of key parts, user interface functions, and mode selection. Within these user-centric application domains, appropriate actuation force and tactile feedback are significant parameters impacting user experience, thereby establishing actuation force as a key specification for selection.
To illustrate, microwave door interlock switches demand precise operating force control to guarantee reliable actuation with minimal user pressure, as excessive force can substantially diminish user comfort and potentially lead to premature wear of mechanical parts with prolonged use. In contrast, micro switches utilized for water level sensing in washing machines must function dependably amidst water fluctuations and impacts, requiring a minimum waterproof rating of IPX7, coupled with consideration of resistance to corrosion, to effectively prevent short circuits and contact degradation due to the intrusion of water or detergents, ultimately ensuring the safe and dependable operation of the appliance.
Furthermore, in line with the increasing emphasis on aesthetics and streamlined design in household appliances, micro switches featuring compact, ultra-thin, and surface mount technology (SMT) configurations offer benefits for enhanced overall device aesthetics, optimized internal volume utilization, and streamlined manufacturing processes.

Specification-Based Micro Switch Selection
Micro Switch Selection for Low-Voltage DC Circuits
In pivotal button control implementations within portable electronic devices, including smartphones and tablets, the internal circuitry typically employs low-voltage direct current (DC) power, with a characteristic voltage range of 3 to 5V. For these implementations, it is crucial to select micro switches with a DC rated voltage (DC micro switch) precisely commensurate with the circuit and to consider their minimum operating voltage to ensure reliable actuation across the device’s entire voltage operating regime. As these implementations primarily facilitate signal transmission and logical control functions, the required rated current of the contacts is typically low, generally within the tens to hundreds of milliamperes to accommodate signal transfer demands.
Nevertheless, user experience is paramount in portable electronic devices, where consistent tactile feedback and operating force of the buttons are critical user experience factors, and even subtle variations can significantly affect user satisfaction. Consequently, micro switch manufacturers must institute stringent process control and quality verification protocols during production to guarantee high consistency and reliability of product performance.
Micro Switch Selection for High-Voltage AC Circuits
For applications within power control systems, particularly as auxiliary contacts in high-voltage circuit breakers or control contacts in relays, micro switches encounter the significant challenge of high-voltage alternating current (AC) environments, often with rated AC voltages reaching several kilovolts. This necessitates exceptionally high insulation performance for these micro switches, requiring adequate creepage distance and clearance, along with adherence to pertinent dielectric withstand voltage standards, to effectively mitigate the risk of insulation failure under high-voltage transients and safeguard the electrical integrity of power control systems.
Furthermore, the intrinsic current zero-crossing phenomenon in AC circuits renders the generation of electric arcs highly probable during the interruption of inductive loads or significant current magnitudes. Consequently, specific micro switches engineered for high-voltage AC applications (AC micro switch) integrate specialized arc suppression methodologies, encompassing the selection of contact materials, optimization of contact geometry, and the implementation of arc quenching chambers, capable of rapidly and effectively extinguishing arcs within the extremely short temporal window of contact separation. This significantly reduces arc-induced erosion and oxidation of the contacts, effectively protecting them, prolonging the switch’s electrical life, and ultimately guaranteeing the safe and stable operation of power control systems.
Micro Switch Selection for Specific Application Scenarios
Micro Switch Selection for High-Temperature Applications
In extremely high-temperature environments such as automotive engine compartments and industrial kilns, micro switches integrated into sensors play a crucial role in monitoring temperature, pressure, or position. Conventional polymer-encased micro switches exhibit significant susceptibility to softening, deformation, reduced mechanical robustness, and degraded electrical characteristics under sustained high-temperature exposure.
Accordingly, for these high-temperature deployments, it is imperative to specify high-temperature micro switches featuring housings fabricated from high heat-resistant ceramics or specialized high-temperature engineering polymers (such as PPS, PBT, etc.), with internal critical metallic and dielectric components subjected to specific thermal conditioning. Furthermore, ensuring that their rated operating temperature envelope encompasses the actual application environment is crucial. This specification guarantees long-term stable and dependable operation even within harsh environments reaching 120℃ or higher, providing real-time and accurate telemetry of critical engine or equipment parameters, and ensuring the precision and reliability of the control system.
Micro Switch Selection for Explosion-Proof Applications
In specialized industrial environments characterized by the presence of flammable and explosive hazardous materials, such as chemical processing plants, petroleum refineries, and mining facilities, the intrinsic safety of electrical equipment is of paramount importance, as any potential source of ignition can precipitate catastrophic events.
When micro switches are intended for use in critical safety applications within these settings, such as valve control, limit safeguarding, and level alarming, it is crucial to rigorously choose explosion-proof micro switches that have been certified by reputable organizations and possess explosion protection levels appropriate for the specific hazardous zone and gas/dust classification, for example, Ex d IIC T6. These micro switches typically feature high-integrity, hermetically sealed metallic enclosures, and their internal electrical and mechanical architectures are specifically engineered to fundamentally preclude the generation of any electrical incendivity and the accumulation of hazardous thermal energy, thereby effectively preventing the micro switch from becoming a potential ignition source and maximizing the safety of on-site personnel and production infrastructure.
To summarize, the accurate selection of micro switches tailored to specific application demands is a systematic engineering process that draws upon diverse fields of expertise. Engineers and designers must holistically assess the intricacies of the application environment, the critical alignment of electrical parameters, and any potential specialized functional needs, while also consulting pertinent industry standards and regulations. This enables them to identify the micro switch component that optimally satisfies application requirements and delivers consistent, dependable performance, thus quietly ensuring the efficient and safe operation of a wide range of equipment in industrial control, electronics, and consumer products, and providing a vital and reliable contribution to the seamless operation of modern technological society.
Accurate specification not only significantly enhances the overall reliability and extends the operational lifespan of equipment but also guarantees the safe and stable operation of systems during critical operational phases, underscoring its strategic and economic import.